船の外面を成す「船形」は、ほとんどが滑らかな曲面構造で作られています。大型タンカーともなると、外面に使われる鋼板は数百枚。その一枚一枚をつなぎ合わせて、美しい流線形の船形が生み出されるのです。では、その曲面はどのようにして作られるのか。実は、一枚一枚が非常に複雑な形状のため、機械だけで生み出すことは不可能です。必要となるのは、熟練技能者の“経験と勘”。厚みのある鋼板を、横と縦の方向へと三次元に曲げていく。この技術を『撓鉄(ぎょうてつ)』と呼び、撓鉄の技を習得するには少なくとも20年の経験が必要だと言われています。
全国的にも稀少なこの技術で、長年評価されてきた当社。業界内でベテランの職人が少なくなる中、しっかりとその技が受け継がれており、大手造船メーカーから安定したご依頼をいただいています。
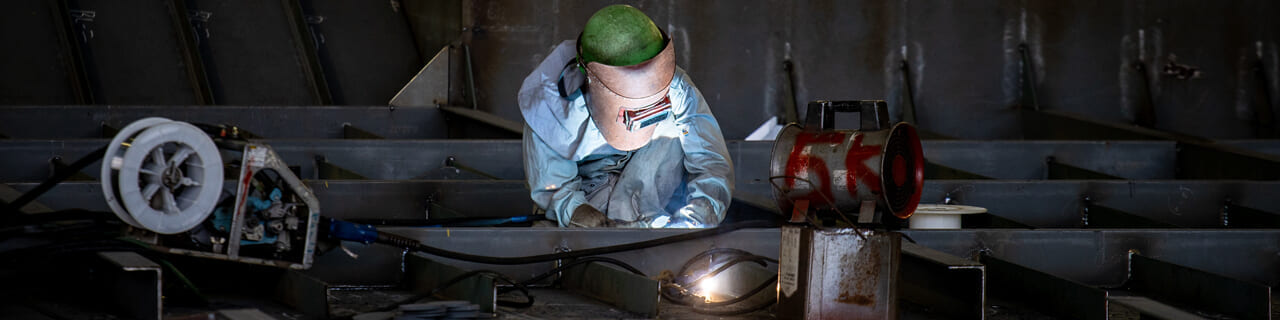
厚さ35㎜の鉄板を、匠の技で優美な曲線に仕上げる
- ホーム
- 船体外板焼き曲げ(撓鉄)
造船の中でも難度の高い『撓鉄(ぎょうてつ)の技』とは
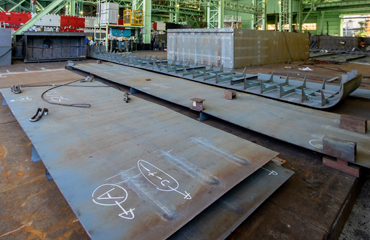
【撓鉄作業の流れ】
①<荒曲げ工程>
プレス機にて、真っ直ぐな鋼板を荒曲げします。
②<焼き曲げ工程>
設計図をもとに組んだ木型に、荒曲げした鋼板を合わせてガスバーナーで加熱。どこをどのくらい熱すればどう曲がるか、知り尽くした職人が手際よく作業を進めていきます。
熱により膨張した鋼板を、今度は水で冷却することで、徐々に流線形の曲面が作られます。
③<検査工程>
焼き曲げした箇所に木型を合わせ、曲がり具合を確認。一度に曲がるわけではないので、何度も焼いて冷やしてを繰り返しながら完成形へと近づけていきます。
④<完成>
完成した外板は、船の部材として造船メーカーへと出荷されます。
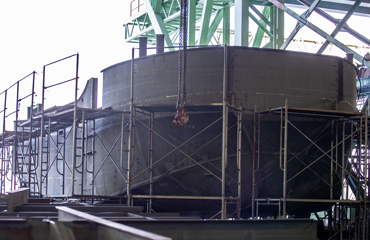
【曲面により異なる“曲げ加工”~冷間曲げ】
船体外板には様々な曲面があるため、その形状に合わせた“曲げ加工”が行われます。たとえば、船体の側面など比較的長く真っ直ぐな部分には、プレス機やローラーが用いられ、船首部や船尾部など複雑な部分は職人の手による『撓鉄加工』が用いられるわけです。
『冷間曲げ』とは、プレス機やローラーなどの機械を使った加工方法のこと。当社では、撓鉄加工の前段階として、まずは冷間曲げにて大まかな形状をつくり、その後ガスバーナーを使った加熱曲げ(撓鉄)工程へと移ります。
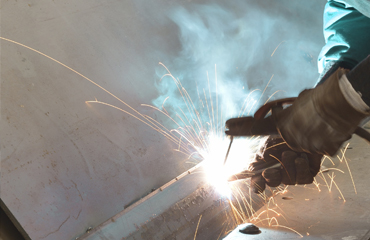
【複雑な曲面をつくる~熱間曲げ(撓鉄)】
熱間曲げ(=撓鉄)は、その名の通り800℃~900℃の高熱により鋼材を曲げる加工方法。冷間曲げに比べ、小さな圧力で加工できるため、より繊細な曲げ加工が可能です。具体的には、鋼板の表面をガスバーナーで加熱すれば、その部分が膨張。そこを冷水で急激に冷やすことで、熱する前よりも鉄が収縮し鋼板が曲がるという仕組みです。この方法は戦後になって生まれたもの。戦艦大和などは、熱ではなく“叩いて曲げる”方法のみでつくられたといいます。撓鉄技能の発達に伴い、造船の精度は格段に向上したと言えるでしょう。
この道40年以上の熟練の技を、若手に継承
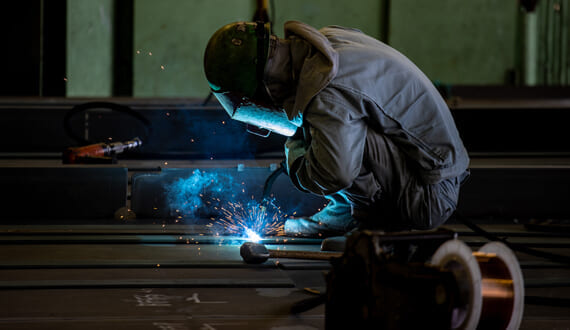
【大手造船メーカーからも信頼される、匠の技】
厚さ35㎜の鋼板を一枚一枚木型に合わせ、ガスバーナーと水で「加熱・冷却」を繰り返しながら徐々に曲げていく地道な作業。そこには、職人が永い年月をかけて身に付けた“経験と勘”が生かされています。というのも、当社には経験40年超えというベテラン職長が在籍。ガスバーナーの火炎の色や、加熱中の鋼板表面の色を見ただけで、最適な入熱量と焼き入れ位置を把握し、絶妙に調整ができる。こうした高い技量があるからこそ、取引先からの依頼が後を経たないのです。
ミリ単位の精度で繊細優美な曲面に仕上げていく、熟練にしか成しえないこの技は当社の財産と言えるでしょう。
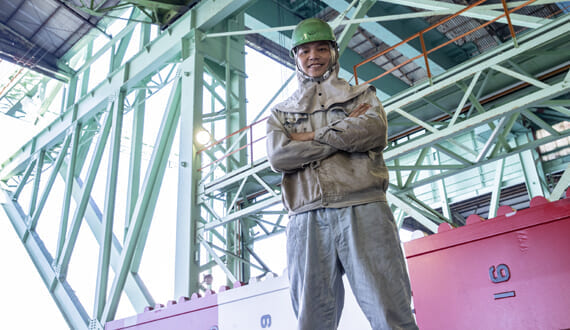
【次世代を担う若手を育て、選ばれる会社へ】
仕上がり次第で、船舶のスピードや燃費、耐久性などが決まる「撓鉄」の技。船体外板焼き曲げ工程は、造船において非常に大きな役割を果たすものです。けれども今、造船業界では熟練技能者の高齢化が進み、撓鉄技能をもつ職人は年々減っていくばかり。技能の継承が最大の課題といっても過言ではありません。
その中で当社では、20代の若手技能者が着実に成長中。ベテラン職長のもとで、焼き曲げのノウハウを基礎からじっくりと技を学んでいます。見据えているのは、20年後の未来。技術革新を進める一方で、伝統的な技の継承にも力を入れ、選ばれ続ける会社を目指していきます。